Как проводится сварка арматуры | Методы | Технология
17 декабря 2021
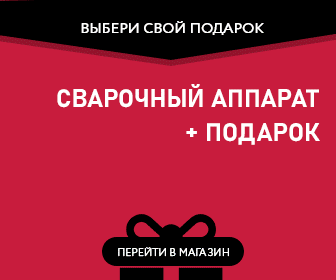
В условиях космоса первый процесс сварки был проведен в далеком 1969 году на корабле «Союз–6». Лишь спустя 15 лет стала возможным сварка в открытом космосе. Ее успешно провели Светлана Савицкая и Владимир Джанибеков в 1984 году.
Но не будем вдаваться в романтику и спустимся пониже, чтобы рассказать вам о способах сварки арматуры и как их выполнить на земле.
Для чего нужны армированные каркасы
Металлические стержни широко используются в строительстве. Массивным сооружениям из бетона необходимо придать стабильность и прочность, для чего создают прочную объёмную решётку из арматуры. Стержни в конструкции каким–то образом нужно закрепить, и для этого используют два способа соединения: связывание проволокой и сварку. Последний метод оказывается наиболее долговечным, доступным по цене и сравнительно несложным.
Как выполнить соединение арматуры
Для того чтобы правильно варить стальные прутки, необходимо понимать особенности материала. Стержни из стальных сплавов разного диаметра от 5 до 80 мм производят гладкими или с оребренной поверхностью с последующей закалкой (в последнее время появились прутки из стеклопластика).
Выбор материала зависит от величины и характера нагрузки, которую будет испытывать конструкция при эксплуатации.
- Оребренные стержни применяют в качестве основного несущего элемента армирования.
- Прутки с гладкой поверхностью используют в качестве вспомогательных для монтажа и ориентации частей каркаса.
Сборка методом сварки должна проводиться точно и быстро, поскольку высокие температуры нарушают структуру металла: закалённая сталь в местах контакта теряет закалку (сплав отпускает).
- Внахлёст с применением электродуговой технологии.
- Тавровым способом (точечная сварка).
- Встык.
Остановимся на каждом методе подробно.
Сварка внахлёст
Выполняется для не слишком нагруженных сооружений с минимальными требованиями к армокаркасу. Для бетонных оснований или конструкций с возможными изгибающими нагрузками способ не подойдёт.
Сварка арматуры внахлёст ведётся в продольном направлении, при этом стержни накладываются один на другой на 15–30 см. Понятно, что чем больше отрезок совмещения, тем прочнее контакт. Сварка выполняется по двум сторонам, что в определённых обстоятельствах может создавать проблемы. Сварщику проще выполнить работу по верхней части, поэтому снизу прочность шва может оказаться недостаточной.
Для того чтобы повысить площадь контакта, обе части стержней необходимо зачистить от ржавчины. В некоторых случаях применяют глубокую шлифовку до получения плоской поверхности. После предварительной подготовки до нужного уровня приступают к сварке арматуры.
Выбор режимов
Настройки аппарата и выбор электрода зависят от диаметра стержней.
Диаметр арматуры, мм |
Сечение электрода, мм |
5–8 |
3,0 |
8–10 |
4,0 |
10–30 |
5,0 |
Параметры сварки по току выставляются более точно:
Диаметр арматуры, мм |
Сила тока, А |
5 |
200 |
6 |
250 |
8 |
300 |
10 |
350 |
20 и выше |
450 |
Технология работы встык
Сварка этим методом наиболее экономична. За счёт отсутствия нахлёста снижается металлоёмкость конструкции и время производства швов, при этом прочность соединения оказывается выше. Явные преимущества метода не уменьшают значение недостатков.
- Сварка арматуры встык не даёт достаточной прочности для сопротивления изгибу.
- Изделия с небольшими диаметрами практически невозможно соединять, поскольку металл в месте контакта перекаливается, и его свойства теряются.
- Работать со стержнями в разных пространственных положениях непросто, и это затрудняет выполнение сварки стыковым методом.
Если все ограничения удаётся обойти (конструкция не рассчитана на изгибающие нагрузки, нужны стержни с большими диаметрами, соединение выполняется в удобном положении), сварку ведут с применением технологии в ванне.
Работа в расплаве
Матрицы для ванны изготавливают самостоятельно или приобретают готовые. Концы прутков помещаются в ёмкость из низкоуглеродистого стального сплава и плавят место стыка одного прутка, подавая ток в пределах 450–550 А. Если процесс сварки арматуры необходимо вести при пониженных температурах, параметры по току поднимают на 15%.
После того как в ванне появится жидкий металл, начинают плавить второй пруток. Процесс плавления ведут попеременно до тех пор, пока жидкий металл полностью не покроет стержни. Затем электродом прогревают место стыка со всех сторон, чтобы остывание происходило наиболее равномерно. После кристаллизации металла два стержня превращаются в монолит.
Место соединения по диаметру соответствует параметрам ванны. Желательно подбирать металлическую ёмкость таким образом, чтобы расстояние до стенок не превышало 1,5–2,0 см.
В процессе сварки арматуры с применением технологии в ванне стальная металлическая форма становится частью соединения. В таком виде место стыка заливается бетоном. Съёмные ёмкости из графита или меди рассчитаны на многократное применение.
- Производство нагруженных фундаментов.
- Изготовление сложных объёмных каркасов.
- Стыковка прутков большого диаметра (более 20 мм).
- Соединение стержней, расположенных в каркасе рядами.
Совмещение прутков может выполняться в горизонтальном и вертикальном положении. Технология сварки арматуры в ванне оказывается наиболее долговечной благодаря монолитному совмещению стержней с высокой степенью однородности шва.
Контактная сварка арматуры тавровым методом
Распространённый приём, широко применяемый в строительстве. Принцип стыковки прутков основан на пропускании тока по цепи, частью которой становятся сами стержни. В месте с наибольшим сопротивлением (участок контакта) металл разогревается и плавится. Концевые части стержней становятся пластичными, благодаря чему после сдавливания возникает неразъёмное соединение.
- Выполняется контактно–точечная сварка арматуры, при которой прутки соединяются внахлёст (сваривание происходит в местах соприкосновения металла).
- В стыковом варианте соединяют торцевые части стержней.
К преимуществам метода относится высокая производительность работ и экономичность за счёт отсутствия расходников. Недостатки тоже есть: сварку каркасов можно вести только в условиях цеха, поскольку в процессе используется мощное и массивное оборудование, способное выдать высокие показатели по току.
Контактно–стыковая сварка арматуры проводится как с непрерывным оплавлением участков стыка, так и с использованием прерывистого прогрева. Первый вариант применяют для армирования стержнями A1 при производстве каркасов нагруженных железобетонных конструкций. Второй метод годится для остальных классов.
Перед началом сварки участки стыков зачищают от ржавчины с помощью металлической щётки. Дефекты металла, например, наплывы, образовавшиеся в процессе резки прутков автогеном, сбивают.
- Величины тока.
- Плотности и усилия контакта на зажимах.
- Продолжительности процесса.
- Длины прутков, выступающих из зажимов.
Выбирая вариант с непрерывным оплавлением, необходимо, чтобы плотность тока оставалась на уровне 10–50 А на каждый мм2. В этом случае продолжительность процесса варьируется в пределах 1–20 с (время зависит от диаметра соединяемых прутков). Сила давления зажимов подбирается в зависимости от сечения и марки стального сплава.
Например, для класса A1 необходимо выдерживать давление в пределах 30–50 МПа, для стержней A2 и A3 следует увеличить усилие до 60–80 МПа. Состояние губок зажимов, удерживающих прутки, должно быть максимально чистым. В процессе работы нужно следить за поверхностями, периодически убирать загрязнения и, если требуется, менять зажимы на новые.
Контроль качества контактного шва выполняется лабораторными методами с предварительной визуальной оценкой. После завершения сварки участок стыка должен быть слегка приплюснутым с небольшими бортиками по краям. Если место совмещения прутков получилось бочкообразным, значит, допущена ошибка в выборе сварочных параметров.
Товары
Характеристики
Получите 500 бонусов, подписавшись на рассылку
Подписаться